Leakage test
Avoid leakages
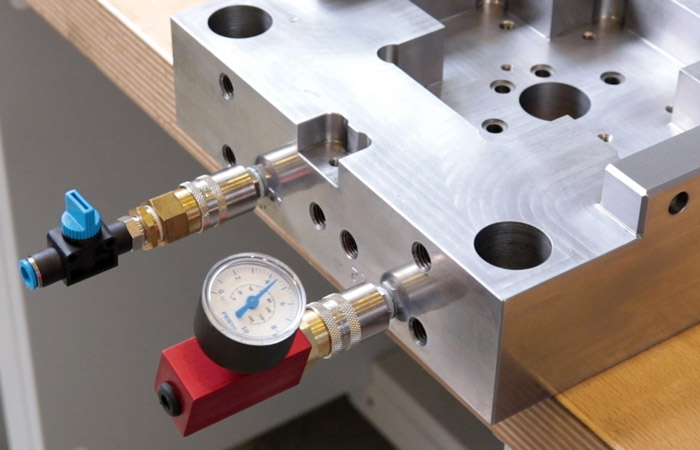
Product properties
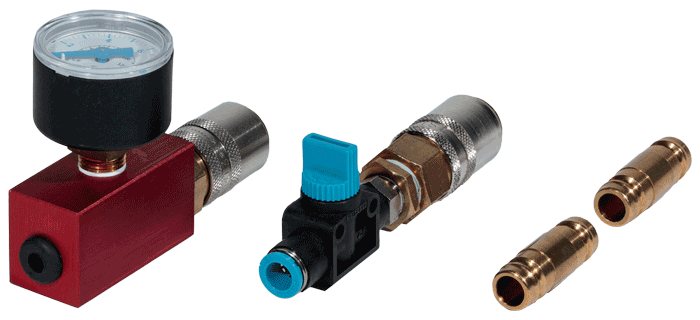
Easy handling
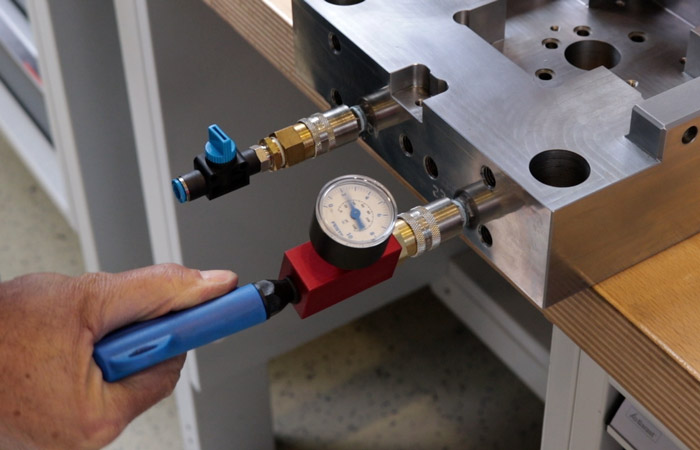
Versions and scope of delivery
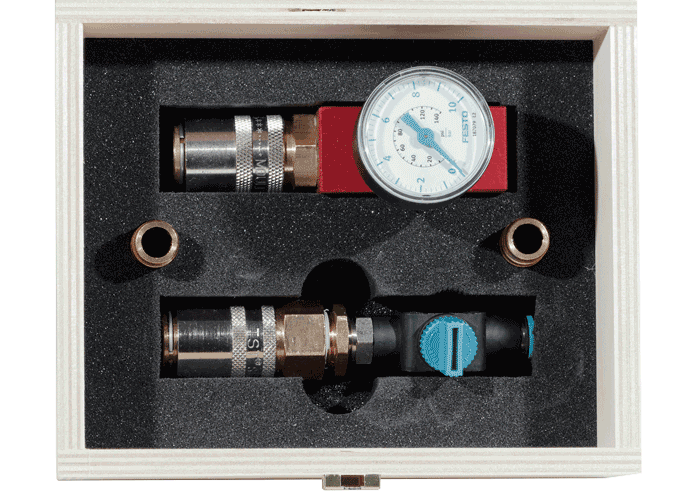
FREQUENTLY ASKED QUESTIONS
The FAQ’s for leakage testing
How high should the test pressure be?
A maximum of 4 bar is sufficient for reliable testing with compressed air.
How long is the testing time?
The larger the volume of the circuit to be tested, the longer the test cycle should be. For 120 cm³ volume, a test time of approx. 60 seconds is sufficient. As a reference value: 120 cm³ volume corresponds approximately to a 4-cavity tool with mould inserts 130 mm x 130 mm and conventional 8 mm holes on one level.
Why is testing with compressed air?
Testing by means of compressed air is cleaner and faster than previous testing methods using the water pump. Air has a 20 times lower viscosity than warm water (80°C). Therefore longer test times are no longer meaningful. The higher viscosity of air would indicate leaks which, if tested with water, are tight.
How does self examination work?
In order to check the unit for leaks from time to time or if necessary, simply connect the inlet and outlet sides using the double nipples supplied. Close the valve and blow in compressed air. Due to the small air volume, a test duration of approx. 30 seconds is sufficient. This ensures that you always have a functional product and reliable test results.
For which connections is the test device suitable?
The integrated quick couplings make the device easy to use for all common profiles. You can obtain the testing device from us suitable for your required coupling series in different nominal widths. Even tools with multi-couplings can be tested. Simply connect one channel at the input and output with the tester and bridge the other channels one below the other. Then the tightness test can be carried out in the same way as for the mono-couplings.
CONTACT US NOW
Ensure a stable production process in your injection moulding shop.
Jochen Schwegler
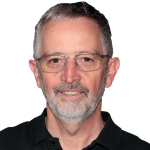
Consultant Plastic Injection Molding/Mold Making/Project Planning
+49(0)7181/4087-217
+49(0)7181/45351
+49(0)152/09 01 11 63
j.schwegler@nonnenmann-gmbh.de