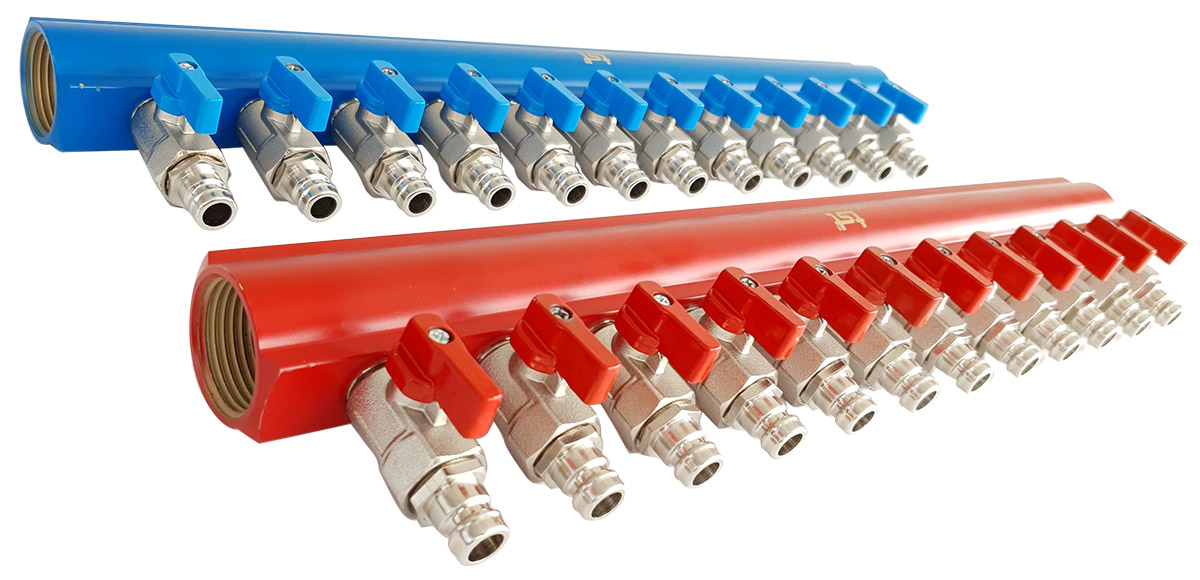
TEMPERING DISTRIBUTORS
THE ADVANTAGES OF PARALLEL HOSING
In plastic injection molding, highly heated liquid plastic is injected into the mold. The injected part should then cool as quickly as possible in order to achieve short cycle times and high quantities.
In serial tubing, starting from the temperature control unit, all temperature control circuits of the mold are connected in series and interconnected with hoses. The temperature control medium (water or temperature control oil) is then fed back to the temperature control unit. This type of tubing can be implemented with little effort and is therefore frequently encountered in practice.
The major disadvantage here, however, is that the tempering medium absorbs more and more temperature on its way through the mold. The molded product is cooled unevenly and is consequently subject to residual stress, which can lead to cracks, i.e. poor quality. The cycle time is also extended, as the cooling process takes more time.
In parallel tubing, two temperature control manifolds are connected between the temperature control unit and the mold. One serves as the supply and the other as the return. The supply distributes the temperature control medium in parallel to the temperature control circuits via its outlets. From each temperature control circuit, the medium is then fed back to the return. In this way, each temperature control circuit receives the desired cooling.
BRASS TEMPERATURE DISTRIBUTORS
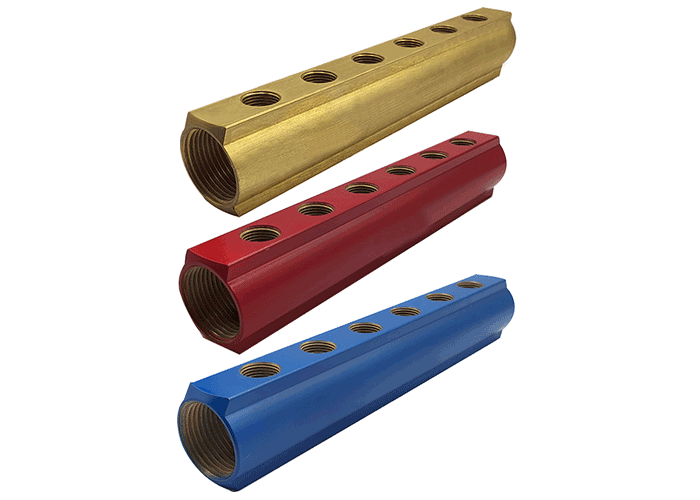
ANODIZED ALUMINUM TEMPERATURE DISTRIBUTORS
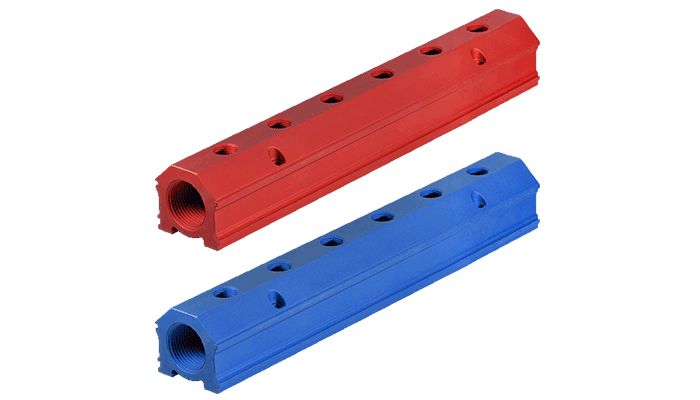
STAINLESS STEEL TEMPERATURE DISTRIBUTOR
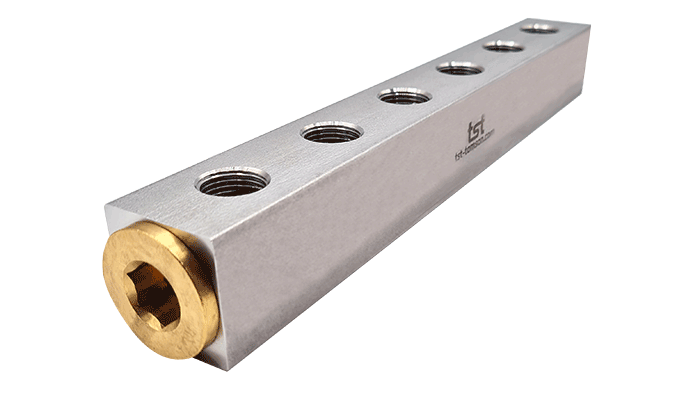
ACCESSORIES
CONTACT US NOW
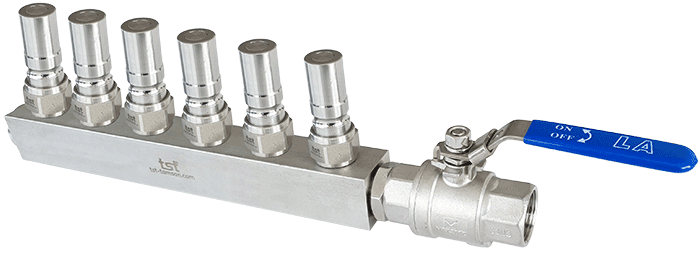